Carbon cycle economy
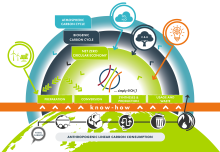
Key technologies
Gasification
In thermochemical conversion by gasification, carbon carriers are converted into a gas containing H2 and CO at temperatures above 700 °C using a gasification agent. This synthesis gas is a basic chemical in the chemical industry and the starting point for a wide range of products. In addition to hydrogen and synthetic fuels, it can be used to produce the platform chemicals alcohols, paraffins, olefins and ammonia. The gasification process, which is usually carried out at high pressures for these applications, was originally developed primarily for the conversion of fossil fuels and used worldwide, but is attracting increasing interest for the material utilisation of waste due to its high flexibility.
Pyrolysis
In pyrolysis, carbon-containing waste is thermally decomposed into combustible gases, oils and solid residues at temperatures of approx. 400 - 600 °C in the absence of air. This requires the addition of heat and can be supported by the use of catalysts. It is an established thermochemical process for the production of oil and wax as well as waste treatment for the recovery of metal and fibres from composite materials. The use of waste-based pyrolysis oil in refinery processes as a substitute for naphtha is a favoured method for chemical recycling, particularly of used plastics.
Research topics
Chemical recycling
Chemical recycling - also known as feedstock recycling - is based on the conversion of carbon-containing waste into chemical building blocks in order to produce new chemical products. This turns waste into resources in the sense of a consistent circular economy and carbon is incorporated into new products instead of being emitted as CO2, as is the case with waste incineration. In this context, we deal with the primary thermochemical conversion of various waste and residual materials through pyrolysis and gasification, including peripheral processes, as well as the technical, socio-ecological and economic evaluation of the entire process chain from feedstock to product. One focus is on the integration of electricity and hydrogen from renewable sources.
Sustainable hydrogen production
Hydrogen plays a central role in the realisation of a climate-neutral economy. The provision of hydrogen itself must be climate-neutral and therefore sustainable. This applies in particular to the hydrogen source and the provision of energy for the production process. Our research focusses on hydrogen production via electrothermal or thermochemical conversion processes. This includes the pyrolytic splitting of methane, which produces so-called "turquoise" hydrogen, and the gasification or reforming of biogenic waste and residual materials with subsequent maximisation of the hydrogen yield.
CO2-Neutral mobility
CO₂-neutral synthetic liquid fuels are a climate-friendly addition to electric and hydrogen mobility. Not only can they directly replace fuels from fossil sources, they can also be mixed with them in any ratio (drop-in capability). This enables a continuous transition to these synthetic fuels, including the utilisation of the existing infrastructure for distribution and sales. A key area of application in the future will be in areas where electric and hydrogen mobility are reaching their limits. This applies in particular to the aircraft fleet, for which liquid fuels will continue to be indispensable in the near future. The focus of our research work is the synthesisation of "green" fuels based on methanol from laboratory to pilot scale, including catalyst and process chain evaluation.
Research projects
Special funding for the Fraunhofer branch "Carbon Cycle Technologies (CCT)" of the Fraunhofer Institute for Ceramic Technologies and Systems IKTS
The Carbon Cycle Technologies (CCT) research group was founded in October 2017 as a branch of the Fraunhofer IMWS. The research objectives of the KKT group focus on the efficient, resource-saving and climate-neutral utilisation of carbon carriers. This development work is carried out in close cooperation with the TU Bergakademie Freiberg. Since 2019, the KKT research group has received start-up funding from the Saxon State Ministry of Science, Culture and Tourism (SMWK) totalling 4.6 million euros, which has been used to purchase extensive equipment, among other things. On 1 January 2023, the Freiberg research group Carbon Cycle Technologies KKT was integrated into the Fraunhofer Institute for Ceramic Technologies and Systems IKTS.
The Fraunhofer Institute for Ceramic Technologies and Systems aims to leverage further synergies in electrolysis, hydrogen and power-to-X technologies and develop sustainable carbon sources for the circular economy with the help of the KKT research group. The aim is to optimise chemical recycling processes such as pyrolysis or gasification and to test these on an industrial scale. Plastics that cannot be mechanically recycled, biomass or mixed fossil waste are broken down into smaller molecules so that they can be reused as synthesis gases, monomers or other intermediate products in the chemical industry. To this end, the researchers operate a pyrolysis platform at the site and - in cooperation with the TU Bergakademie Freiberg - gasification plants to investigate various issues: Which waste fractions can be converted into which type of base materials? How must the processes be operated in order to avoid corrosion or caking or to achieve a certain purity of the products? And finally, the question of economic efficiency. In this way, various technologies can be adapted and evaluated for industrial partners and transferred into customised solutions for closing carbon cycles. KKT's research objectives focus on the efficient, resource-saving and climate-neutral utilisation of carbon carriers. If the recycling processes mentioned are combined with electrochemical conversion processes such as high-temperature electrolysis or synthesis processes such as Fischer-Tropsch synthesis, higher-value products such as synthetic paraffin can be produced and high levels of efficiency can be achieved. Only the coupling of material, energy and heat flows in total leads to process concepts that offer significant added value compared to previous approaches. With the expanded expertise in the field of carbon cycle technologies, the company is now in a position to provide new raw material and energy resources for a green industry.
Term: 2019- 2024
"This measure is co-financed by tax funds on the basis of the budget adopted by the Saxon State Parliament"
Advanced materials engineering for arc plasma-assisted production of hydrogen-containing syngas for clean energy utilisation
Challenge: In the context of plasma-assisted gasification of waste, especially with water vapour plasma for hydrogen production, high electrode erosion rates lead to uneconomical plant operating times.
Our project: Development of advanced electrode materials with high mechanical and chemical resistance to reduce the erosion of the electrodes under the influence of the arc and reactive gases. Furthermore, new electrode geometries with a monolithic three-dimensional structure are being developed and manufactured using additive processes in order to achieve better heat transfer during water cooling of the electrodes and to minimise thermally induced degradation of the electrodes.
Partners: AGH University of Krakow, DTU Technical University of Denmark, DBI Virtuhcon GmbH
Funding: European Regional Development Fund (ERDF), Sächsische Aufbaubank (Reference Number: project11426, funding code: 100728552)
Term: 09/2024 - 08/2027
Problem: The maritime sector is responsible for 3% of global greenhouse gas emissions, which are generally considered difficult to avoid. Nevertheless, shipping is irreplaceable in freight transport and also in passenger transport. Climate-friendly solutions must therefore be developed.
Solution variants: Alternative drive concepts such as electromobility can hardly be implemented in the maritime sector, especially for large ships and long distances. Support from wind power (sails) and a reduction in speed can make a contribution, but are not enough. Alternative fuels are an option, but they drive up the traditionally high proportion of fuel in the overall costs even further. Furthermore, ships have a long service life, so the solutions should also be applicable to the existing fleet as far as possible. Carbon capture, i.e. the separation of CO2 from the exhaust gases, is therefore also considered a possible part of the solution.
Our project: In the CCS on Ships project, various concepts for CO2 separation are being analysed and compared for different types of ship. The overall system consisting of ship, capture unit and storage is modelled in system simulations. CO2 handling on board and in the harbour is also part of the project.
Partner: Large Engines Competence Center Graz (LEC), Chair of Thermodynamics at the Ruhr University Bochum
Funding: Industrial Collective Research (IGF): Research Association for Internal Combustion Engines (FVV) / Federal Ministry of Economics and Climate Protection (BMWK)
Term: 01 September 2022 - 30 September 2024
More information: OnePager (PDF)
Demonstrating a Circular Carbon Economy in Transport along the Value Chain:
Development of the olefins-to-jetfuel process as a highly innovative stage in the production of paraffin from renewable methanol
Challenge: Thanks to their specific properties, liquid fuels are also of great importance in many areas of the energy sector in the long term. While electricity is a preferred alternative as an energy source, especially for cars and light lorries in cities, low-GHG liquid fuels are needed in particular for heavy goods transport over long distances, aviation and maritime transport, as well as for petrochemical precursors, lubricants and other products. The EwOPro project focuses on the highly innovative olefins-to-jetfuel process as the centrepiece of the methanol-to-jetfuel route.
Our project: The main objective of EwOPro is the detailed investigation of the process for converting olefins to paraffins or oligomers in the corresponding chain. oligomers in the corresponding chain length and branching within the methanol-to-jetfuel process, which is relevant for the target product fraction paraffin and the co-products high-octane/aromatic-free petrol and diesel/fuel oil. In particular, the focus is on knowledge-based catalyst development and optimisation of the process technology parameters of the individual process stages methanol-to-olefins (MtO), olefin oligomerisation (OtJ) and hydrogenation, as well as their combination.
At the Chair of Energy Process Engineering, the STF+ pilot plant, which has been upgraded for operation in MtO mode, is being expanded to include scaled-up OtJ process stages. The oligomerisate produced during the subsequent experimental investigations for process optimisation will be made available to the project partners for hydrogenation, fractionation and fuel tests.
Partners: CAC Engineering GmbH, DBI Gas- und Umwelttechnik GmbH, Fraunhofer Institute for Ceramic Technologies and Systems IKTS (funded project partners) and other associated project partners
Funding: Federal Ministry of Economics and Climate Protection (BMWK), FKZ 03EI3083C
Term: 03/2023 - 08/2026
Recycling of industrial polycarbonate waste through selective pyrolysis; sub-project: Investigation and optimisation of the pyrolysis of polycarbonate on a pilot plant scale
Vision: The vision of the PC2Chem project is to establish a chemical recycling process for polycarbonate waste that can be used to produce starting chemicals for polycarbonate products from waste collected on a large scale. This avoids the use of fossil raw materials and saves energy-intensive process steps.
Our project: In particular, the project involves the development of a pyrolysis technology for the chemical conversion of polycarbonate waste, especially PC/ABS blends, into high-quality products such as bisphenol A (BPA) and styrene. In addition, selective pyrolysis will also be used to process additivated PC and PC composites. The high-quality molecules obtained will be reused for the production of PC. The main objective of Fraunhofer IKTS is the detailed investigation of the pyrolysis of various polycarbonates on a pilot plant scale. For this purpose, experimental investigations are carried out in a batch pyrolysis plant and in a continuously operating pyrolysis rotary kiln in order to determine process parameters for a maximum yield of valuable components. The investigations are supported by instrumental-analytical methods for the fundamental investigation of the reactions of different PC qualities during pyrolysis.
Partner: Covestro AG
Funding: Federal Ministry of Economics and Climate Protection (03EI5007B)
Term: 01/2022 - 12/2024
Thermochemical phosphorus recovery under highly reducing conditions with consideration of the CO2 balance
Challenge: From 2029, many sewage treatment plant operators will be obliged to recover phosphorus from sewage sludge and make it available to the economic cycle again. In order not to emit the carbon contained as CO2 but to return it to the carbon cycle, incineration of the sewage sludge is out of the question.
Our project: Basic investigations for the combined recovery of phosphorus and carbon from sewage sludge using allothermal gasification. To this end, the necessary conditions for phosphorus release into the gas phase are identified and an economically viable phosphorus recovery concept is developed, which is verified with laboratory tests and gasification trials on a pilot plant scale.
Partners: RWE, TAF, PreZero Pyral GmbH, DBI Virtuhcon
Funding: Federal Ministry for Economic Affairs and Climate Protection (03EE5086)
Term: 09/2021 - 06/2025
Renewable fuels from green refineries of the future
Challenge: To date, renewable fuels for road, air and sea transport cannot be produced selectively via a single process route. They are usually produced in different proportions together with other by-products.
Our project: The REF4FU project aims to develop, validate and evaluate sustainable refinery concepts that can be used to meet the future demand for renewable liquid fuels. Renewable methanol, Fischer-Tropsch hydrocarbons and pyrolysis oils will be used to produce, test and evaluate the fuels that are currently used in fleets and will be required in the foreseeable future using scalable technologies. The research work at the Chair of Energy Process Engineering will also focus on the production of larger quantities of oligomerisate for the project partners, for which liquid gas dosing and product separation will be retrofitted at the pilot plant.
Partners: DBFZ Deutsches Biomasseforschungszentrum gGmbH, German Aerospace Centre, Karlsruhe Institute of Technology, CAC Engineering GmbH, EDL Anlagenbau GmbH, INERATEC GmbH (funded project partners) and other associated project partners
Funding: Federal Ministry for Digital and Transport Affairs (BMDV), FKZ 16RK24001E
Term: 12/2022 - 11/2025
Prediction of pollution up to the cold end of the flue gas path (VeRa)
Challenge: As part of the Paris Agreement at the 2015 UN Climate Change Conference, Germany committed to reducing greenhouse gas emissions by 55% by 2030 and by 80% by 2050 compared to 1990 levels. From 2050, energy generation is to be almost completely decarbonised. At the same time, the security of energy supply is to be guaranteed, existing energy infrastructure utilised and negative social impacts avoided. Among other things, this can be achieved by gradually replacing fossil fuels with biogenic residues in existing thermal power plants.
Our project: The aim of the project is to contribute to the energy transition by gradually replacing the predominantly fossil fuels used in thermal power plants with residual materials (biomass, waste, etc.). The participating partners are investigating various substitute fuels for use in the power plant process. In particular, TUBA Freiberg is working on the chemical-mineralogical characterisation of different input materials, the categorisation of interactions between ash formers and the release behaviour of process-relevant elements in a simulated process atmosphere using ETV-ICP-OES.
Partners: University of Stuttgart, Forschungszentrum Jülich GmbH, GTT-Technologies, RECOM Services GmbH, Lausitz Energie Kraftwerke AG, RWE Power AG, RWE Generation SE, EnBW Energie Baden-Württemberg AG, Clyde Bergemann GmbH, GE Boiler Deutschland GmbH
Funding: Federal Ministry of Economics and Climate Protection (03EE5064C)
Term: 09/2021 - 09/2025
From waste to raw material - green molecules for chemistry
Vision: Development of comprehensive recycling of plastic-containing waste without loss of carbon through interlocking, networked processes while maximising the preservation of existing chemical structures. Evaluation of innovative recycling technologies for complex waste, with which high-quality recyclates and circular raw materials can be obtained.
Our project: The project will develop and demonstrate a holistic, entropy-based evaluation model that reorganises the previously process-led recycling chain into a material-led chain. Entropy as a measure of the disorder of a system is used to describe the success of recycling. A model based on Shannon entropy or statistical entropy, which is already used for mechanical recycling processes, is also adapted and further developed for chemical recycling.
Partners: Fraunhofer IKTS, Fraunhofer IMWS, Fraunhofer IWKS, Fraunhofer LBF, Fraunhofer IVV, Fraunhofer IOSB, Fraunhofer FHR, Fraunhofer IZFP
Funding: Fraunhofer internal project (lead project)
Term: 01/2021 - 12/2024
- ZIK Virtuhcon
- Erzgebirge - new landscape, new opportunities
- Methanol-to-Gasoline - MTG (sub-project B3 of the TU BAF in the joint research project "C3-Mobility: Closed Carbon Cycle-Mobility: Climate-neutral fuels for the transport of the future"), funding by BMWK (funding code 03EIV021A), project partners BMW, CAC, FEV, Ford, Opel, Shell, VW and others. a., Duration 09/2018-12/2021
- Construction and operation of an STF+ test facility for the production of petrol from renewable methanol and investigations into the fuel quality of future synthetic fuels (TUBAF sub-project in the Kopernikus project P2X: "Research, validation and implementation of 'Power-to-X' concepts"), funded by BMBF (funding code 03SFK2M1), Audi, CAC, OMV, Shell and VW (third-party funders), duration: 09/2016-08/2019