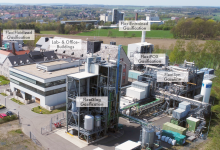
Our range of equipment, from pilot to demo scale, is unique for a university. Together with our comprehensive laboratory equipment, this allows us to conduct research from the basics through to application.
Large systems
The FlexiSlag is a next generation fixed bed slag gasifier designed for high flexibility in feedstocks. It offers variable gas qualities for hydrogen application, syngas application (i.e. low dust, free of tar and phenol, low CxHy) or SNG and liquid products (i.e. low dust, rich in light oil and CxHy). It also has high heat and cold gas efficiency, low oxygen and vapour consumption and virtually no carbon loss. Furthermore, the environmental impact is minimal as the impurities are contained in the vitrified slag. i.e. vitrified slag.
Highlight
Makes it possible to utilise mixed, contaminated and difficult carbonaceous waste that is not suitable for mechanical recycling and pyrolysis as a secondary raw material for chemical production.
The "FlexiSyn Gasoline" is a plant for demonstrating the production of high-octane petrol. Originally, the synthesis route was divided into two steps: Conversion of synthesis gas (produced by ATR treatment of natural gas) into methanol, followed by the subsequent innovative isothermal synthesis process of methanol to gasoline (MtG). Today, only the petrol production is operated with renewable methanol. The technology partner is CAC Engineering GmbH (formerly Chemieanlagenbau Chemnitz GmbH).
Highlight
Project DeCarTrans (demonstration of a circular carbon economy along the value chain) 2023-2026: Production of around
380,000 litres of synthetic petrol from renewable methanol for material, emissions and fleet tests by project partners/selected end users
FlexiPOX plant for partial oxidationThe FlexiPOX plant is designed for the high-pressure partial oxidation of gaseous and liquid hydrocarbons. It can be operated in autothermal catalytic reforming mode (ATR) or as an autothermal non-catalytic partial oxidation mode for natural gas (gas-POX) or liquid hydrocarbons such as oil residues from refineries or pyrolysis oil from chemical recycling (MPG or oil-POX).
Highlight
Unique optical devices enable real-time determination and verification of flame conditions under high-temperature and high-pressure operating conditions with customised burners.
The FlexiEntrained gasification system (GSP process) is an entrained-flow gasifier with a water-cooled cooling screen, a full spray water quench for gas cooling, a Sulferox system for desulphurisation and a waste water treatment system. It is operated with pulverised or liquid (slurry) feedstock. The synthesis gas produced is free of hydrocarbons and contains only a very small proportion of methane. It is capable of converting a wide range of carbon feedstock into a high quality, tar-free syngas and vitrified slag that is environmentally neutral. It also has a commercial-scale pneumatic feed test rig.
Highlight
The technology for converting coal into chemicals is now widely used commercially. More than 60 carbon feedstocks (including various types of waste materials) have been tested in over 100 test campaigns at the Freiberg plant.
The low-temperature gasification plant (LTG) is a continuous pyrolysis plant for converting various carbon-rich biomass or waste into pyrolysis coke and pyrolysis gas containing tar/oil. It can be operated fully electrically in allothermal mode or autothermally with agents to provide heat for pyrolysis. The LTG plant is part of the Fraunhofer IKTS pyrolysis platform.
Highlight
The IKTS pyrolysis platform serves both: the conversion of feedstock to char or to liquid products at a relevant scale.
Catalytic tribo-chemical (CTC) pyrolysis technology is used to convert various carbonaceous wastes into pyrolysis oil as a feedstock for steam crackers. The technology partner is Carboliq GmbH. The CTC plant is part of the Fraunhofer IKTS pyrolysis platform.
Bench-scale systems
The FlexiSlag is a next generation fixed bed slag gasifier designed for high flexibility in feedstocks. It offers variable gas qualities for
hydrogen application, syngas application (i.e. low dust, free of tar and
phenol, low CxHy) or SNG and liquid products
(i.e. low dust, rich in light oil and CxHy). It also has high heat and cold gas efficiency, low oxygen and vapour consumption and virtually no carbon loss. Furthermore, the environmental impact is minimal as the impurities are contained in the vitrified slag.
i.e. vitrified slag.
Highlight
Makes it possible to utilise mixed, contaminated and difficult carbonaceous waste that is not suitable for mechanical recycling and pyrolysis as a secondary raw material for chemical production.
The "FlexiSyn Gasoline" is a plant for demonstrating the production of high-octane petrol. Originally, the synthesis route was divided into two steps: Conversion of synthesis gas (produced by ATR treatment of natural gas) into methanol, followed by the subsequent innovative isothermal synthesis process of methanol to gasoline (MtG). Today, only the petrol production is operated with renewable methanol. The technology partner is CAC Engineering GmbH (formerly Chemieanlagenbau Chemnitz GmbH).
Highlight
Project DeCarTrans (demonstration of a circular carbon economy along the value chain) 2023-2026: Production of around
380,000 litres of synthetic petrol from renewable methanol for material, emissions and fleet tests by project partners/selected end users
FlexiPOX plant for partial oxidationThe FlexiPOX plant is designed for the high-pressure partial oxidation of gaseous and liquid hydrocarbons. It can be operated in autothermal catalytic reforming mode (ATR) or as an autothermal non-catalytic partial oxidation mode for natural gas (gas-POX)
or liquid hydrocarbons such as oil residues from refineries or pyrolysis oil from chemical recycling (MPG or oil-POX).
Highlight
Unique optical devices enable real-time determination and verification of flame conditions under high-temperature and high-pressure operating conditions with customised burners.
The FlexiEntrained gasification system (GSP process) is an entrained-flow gasifier with a water-cooled cooling screen, a full spray water quench for gas cooling, a Sulferox system for desulphurisation and a waste water treatment system. It is operated with pulverised or liquid (slurry) feedstock. The synthesis gas produced is free of hydrocarbons and contains only a very small proportion of methane. It is capable of converting a wide range of carbon feedstock into a high quality, tar-free syngas and vitrified slag that is environmentally neutral. It also has a commercial-scale pneumatic feed test rig.
Highlight
The technology for converting coal into chemicals is now widely used commercially. More than 60 carbon feedstocks (including various types of waste materials) have been tested in over 100 test campaigns at the Freiberg plant.
The low-temperature gasification plant (LTG) is a continuous pyrolysis plant for converting various carbon-rich biomass or waste into pyrolysis coke and pyrolysis gas containing tar/oil. It can be operated fully electrically in allothermal mode or autothermally with agents to provide heat for pyrolysis. The LTG plant is part of the Fraunhofer IKTS pyrolysis platform.
Highlight
The IKTS pyrolysis platform serves both: the conversion of feedstock to char or to liquid products at a relevant scale.
Catalytic tribo-chemical (CTC) pyrolysis technology is used to convert various carbonaceous wastes into pyrolysis oil as a feedstock for steam crackers. The technology partner is Carboliq GmbH. The CTC plant is part of the Fraunhofer IKTS pyrolysis platform.
Highlights der Labor-Ausstattung
Comprehensive Gas Chromatography is an instrumental-analytical method that is particularly used for the analysis of complex mixtures of organic compounds.
Software
- AutoCAD
- AutoCAD P&ID
- Autodesk Inventor
- SolidWorks
- Aspen Engineering Suite: Aspen Plus, Aspen Dynamic, Aspen Custom Modeler, Aspen HYSYS
- Belsim Vali
- MathCAD
- MATLAB
- Origin
- Statgraphics
- Python
- MySQL database
- modeFrontier
- GaBi
- FactSage
- SimuSage
EVT Brochure
You can find more detailed information about our equipment in our brochure: