AddWasserstoff – Nachhaltige additiv gefertigte Hochtemperaturmaterialien für Wasserstoffprozesse
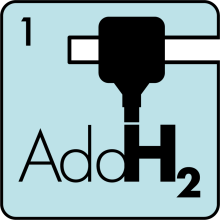
Project management
- Prof. Dr.-Ing. habil. Christos Aneziris (coordinator)
- Prof. Dr.-Ing. Tobias M. Fieback
- Prof. Dr.-Ing. Hartmut Krause
- Prof. Dipl.-Ing. Björn Kiefer, Ph.D.
Project assistant
- Dr.-Ing. Florian Kerber (IKFVW)
- Katrin Markuske, M.Sc. (TTD)
- Deepak Varma Thota, M.Sc. (GWA)
- Siddhi Avinash Patil, M.Sc. (IMFD)
Project duration
1 January 2024 to 31 December 2026
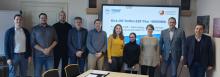
About the research project
The central objective of ESF junior research groups is the interdisciplinary, technical and social qualification of young university graduates. This training initiative aims to utilise synergy effects, particularly in the context of energy, environmental, materials and engineering sciences, and to generate innovative ideas for establishing companies in Saxony.
The ESF project "AddWasserstoff - Nachhaltige additiv gefertigte Hochtemperaturmaterialien für Wasserstoffprozesse" has a duration of three years (01.01.2024 - 31.12.2026) and is dedicated to novel research approaches in the field of sustainable materials for the hydrogen energy industry.
The scientific and technological goal of the "AddWasserstoff" project is to optimise typical high-temperature components for H2 use. To this end, an additive manufacturing process is to be used to specifically combine closed micropores in the microstructure with functional macro-cavities in order to produce highly resistant components. The project aims to conceptualise, design, manufacture and validate innovative demonstrator components. These components are to be based on a corrosion and thermal shock-resistant material and integrated into a component system for the Saxon industry. The project aims to make a significant contribution to hydrogen technology in the energy industry in order to support a stable, green and sustainable economy.
In order to enable model-supported development of the component geometry in micro and macro design for practical application, the chemical, thermal and thermo-mechanical properties of 3D-printed aluminium oxide materials are recorded and evaluated under high-temperature operating conditions. The data required for this is generated by experimentally determining the mechanical and thermophysical properties in various high-temperature tests under different H2 combustion gas atmospheres. These test series include both long-term stress scenarios and different thermal-cyclical stresses on prototype burner components in the near-flame range.
To this end, three young female scientists and one young male scientist from the IKFVW, TTD, GWA and IMFD professorships are working closely together to utilise their respective expertise and resources to achieve the goals of the project. For interdisciplinary research, the chairs are also cooperating in the Centre for Efficient High Temperature Material Conversion ZeHS.
This holistic approach makes it possible to jointly develop theoretical relationships and corresponding material models. Finally, innovative design principles for highly resistant, additively manufactured burner components based on multi-layer ceramics will be developed. These principles are not only relevant for use in hydrogen processes, but are also of outstanding importance in other high-temperature applications, such as in chemistry, metallurgy and energy technology.
The project aims to combine experimental and simulative approaches, focussing in particular on the following areas:
- Filament production - fused filament fabrication
- Sample investigation and structure functionalisation
- Deduction of characteristic fields and change in material properties after weathering
- Development, production and testing of a demonstrator component
- Determination of the thermophysical material data of the original undamaged and aged samples: Temperature and thermal conductivity, density, thermal expansion and specific heat capacity
- Studies with pure hydrogen with regard to the kinetics of damage and gas incorporation
- Equipment adaptations/extension for sorption measurements with H2 combustion atmospheres
- Studies with hydrogen combustion atmospheres with regard to the kinetics of damage and gas incorporation
- Long-term ageing measurement campaigns
- Thermal shock investigations
- Development of design principles for multi-layer materials
Simulative prediction of hydrogen-influenced damage effects in Al2O3
- Identification of the main influencing variables and failure mechanisms with regard to property changes during long-term ageing and thermal shock
- . property changes during long-term ageing and thermal shock
- Extension of the models and the simulation tool
- Simulations for systematic parameter studies and sensitivity analyses
- Numerical investigations of the demonstrator component (additively manufactured burner nozzle)
