INBAF - Innovative component and material design for additive manufacturing
The aim of the ESF-funded IN-BAF project is to take a holistic and application-oriented approach to the entire production chain of additively manufactured metal components using a powder bed-based process. High-alloy steels are used as the material for the project. The focus is particularly on improving the service life properties through the targeted introduction of minority alloys and surface post-treatment.
Specifically, the IN-BAF project is investigating the entire process chain of alloy development, powder production, additive manufacturing in two different processes as well as surface post-treatment, optimisation and service life testing of the components produced in this way. Four junior researchers from three institutes at TU Bergakademie Freiberg are working closely together to analyse not just one building block in the production chain, but the interaction of all production steps.
The Institute of Iron and Steel Materials (IEST) is responsible for the targeted adaptation of steels and powder production, while the Institute of Materials Technology (IWT) characterises the printed material statically and cyclically. The Institute of Machine Elements, Design and Production (IMKF) is responsible for analysing the surface post-treatment, optimising an application component and testing the operational stability of this component.
The printing processes electron beam melting (EBM) at IWT and laser beam melting (SLM) at IMKF are used.
Interested in a specific area? Feel free to read the detailed descriptions of the individual work packages below!

Project management
- Prof. Dr Matthias Kröger (coordinator)
- Prof. Dr Henning Zeidler
- Prof. Dr Olena Volkova
- Prof. Dr Horst Biermann
Young researchers
- Dr Kristina Navickaite (Group Leader, IMKF-AM)
- Dipl. Ing. Jenny Köckritz (IMKF-ME)
- M. Sc. Anastasiia Sherstneva (IEST)
- Dipl. Ing. Stefan Langenhahn (IWT)
Project duration
01.01.2023 - 31.12.2024
Work packages
In work package 1, steel powder is to be produced for successful use in additive manufacturing. The IEST has its own atomisation plant for this purpose, in which the starting material and process parameters are varied. The aim is to achieve an optimal composition, powder morphology and particle size. Minority alloying elements are varied for this purpose.
A powder for additive manufacturing must be free-flowing, but must not vaporise at the first energy input. It must form a favourable microstructure under the production conditions of additive manufacturing and should not tend to form typical printing defects such as paint-of-fusion defects. In addition to SEM images of the powder, the particle size composition and viscosity are therefore also measured.
Contact person: Anastasiia Sherstneva
In work package 2, samples with existing and the newly developed metal powders are printed at the IWT using electron beam melting (EBM). These samples are characterised in detail with regard to the formed microstructure, defects, static and cyclic properties.
The fatigue behaviour will be investigated on untreated ("as-built") samples and samples treated with plasma electrolytic polishing (see work package 3). The results obtained in this way will then be transferred to additively manufactured components in work package 4.
Contact: Stefan Langenhahn
Work package 3 investigates the surface finishing of additively manufactured components. Surface finishing is a very important topic in additive manufacturing, as unmachined parts usually have poor surface quality, which can lead to reduced strength and service life. However, additively manufactured components often show undercuts, cavities or fine structures, which is why conventional surface treatments such as grinding or milling are rarely possible. Plasma electrolytic polishing (PeP) is used in this work package. Optimum process parameters must be found for this, which, for example, smooth the EBM fatigue samples from work package 2 in the best possible way. The improved surface is characterised, for example, non-destructively using optical means or cross-sections and SEM images.
In work package 3, samples and components are also produced at the IMKF-AM using selective laser melting.
Additive manufacturing is still a young field, but is already being used in industry in many areas that are also at risk of failure. It is therefore important to examine not only standardised samples, but also a realistic component. Additive manufacturing is often used for topology-optimised components because their geometry usually cannot be manufactured conventionally - topology optimisation and additive manufacturing are mutually dependent.
In work package 4, the knowledge gained from work packages 1-3 is applied to a practical component. This component will be topology-optimised for production and service life. The material parameters determined in work package 2 and the findings on the expected surface area obtained in work package 3 are incorporated into the numerical analyses. The components are then manufactured using EBM and SLM and tested for their fatigue strength in a specially developed test rig. This allows the findings obtained at sample level to be directly compared with practical applications.
Contact: Jenny Köckritz
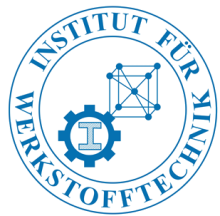
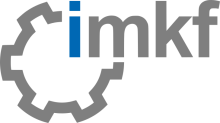
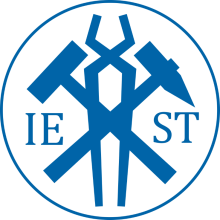