INBAF - Innovatives Bauteil- und Werkstoffdesign für die additive Fertigung
Das Ziel des ESF-geförderten Projektes IN-BAF ist eine ganzheitliche und anwendungsnahe Betrachtung der gesamten Fertigungskette von additiv gefertigten Metallbauteilen im pulverbettbasierten Verfahren. Als Werkstoff werden für das Projekt hochlegierte Stähle angewandt. Dabei stehen besonders die Verbesserung der Lebensdauereigenschaften mittels gezielter Einbringung von Minoritätslegierungen und Oberflächennachbehandlung im Fokus.
Konkret wird im Projekt IN-BAF die komplette Prozesskette von Legierungsentwicklung, Pulverherstellung, additiver Fertigung in zwei verschiedenen Verfahren sowie Oberflächennachbehandlung, Optimierung und Lebensdauerprüfung der so hergestellten Bauteile untersucht. Dafür arbeiten vier Nachwuchsforschende aus drei Instituten der TU Bergakademie Freiberg eng zusammen, um nicht nur einen Baustein in der Fertigungskette, sonders das Zusammenspiel aller Fertigungsschritte zu betrachten.
So findet die gezielte Anpassung der Stähle und die Pulverherstellung am Institut für Eisen- und Stahlwerkstoffe statt (IEST), während das Institut für Werkstofftechnik (IWT) den gedruckten Werkstoff statisch und zyklisch charakterisiert. Das Institut für Maschinenelemente, Konstruktion und Fertigung (IMKF) ist für die Betrachtung der Oberflächennachbehandlung, die Optimierung eines Anwendungsbauteils sowie die Betriebsfestigkeitsprüfung dieses Bauteils zuständig.
Es werden die Druckverfahren Elektronenstrahlschmelzen (EBM) beim IWT und Laserstrahlschmelzen (SLM) beim IMKF angewandt.
An einem bestimmten Bereich interessiert? Lesen Sie sich gern die detaillierteren Beschreibungen der einzelnen Arbeitspakete unten durch!

Projektleitung
- Prof. Dr. Ing. Matthias Kröger (Koordinator)
- Prof. Dr.-Ing. Henning Zeidler
- Prof. Dr.-Ing. Olena Volkova
- Prof. Dr.-Ing. Horst Biermann
Nachwuchsforschende
- Dr. Kristina Navickaite (Gruppenleiterin, IMKF-AM)
- Dipl. Ing. Jenny Köckritz (IMKF-ME)
- M. Sc. Anastasiia Sherstneva (IEST)
- Dipl. Ing. Stefan Langenhan (IWT)
Projektlaufzeit
01.01.2023 – 31.12.2024
Arbeitspakete
In Arbeitspaket 1 sollen Stahlpulver für den erfolgreichen Einsatz in der additiven Fertigung produziert werden. Am IEST ist dafür eine eigene Verdüsungsanlage vorhanden, in der Ausgangsmaterial und Prozessparameter variiert werden. Ziel ist es, eine optimale Zusammensetzung, Pulvermorphologie und Partikelgröße zu erreichen. Dafür werden u.a. Minoritätslegierungselemente variiert.
Ein Pulver für die additive Fertigung muss fließfähig sein, darf aber nicht beim ersten Energieeintrag verdampfen. Es muss unter den Fertigungsbedingungen der additiven Fertigung ein günstiges Gefüge ausbilden und sollte nicht dazu neigen, typische Druckfehler wie z.B. Lack-of-Fusion Defekte auszubilden. Daher werden neben REM Aufnahmen der Pulver auch die Partikelgrößenzusammensetzung und Viskosität gemessen.
Ansprechpartnerin: Anastasiia Sherstneva (Anastasiia [dot] Sherstneva [at] iest [dot] tu-freiberg [dot] de)
Im Arbeitspaket 2 werden am IWT Proben mit bestehenden und den neu entwickelten Metallpulvern mittels Elektronenstrahlschmelzen (EBM) gedruckt. Diese Proben werden bezüglich des ausgebildeten Gefüges, Fehlstellen, statischer und zyklischer Eigenschaften detailliert charakterisiert.
Das Ermüdungsverhalten wird an nicht überarbeiteten („as-built“) und mit Plasmaelektrolytischem Polieren überarbeiteten Proben (siehe Arbeitspaket 3) untersucht. Die so gewonnenen Ergebnisse werden anschließend im Arbeitspaket 4 auf additiv gefertigte Bauteile übertragen.
Ansprechpartner: stefan [dot] langenhan [at] iwt [dot] tu-freiberg [dot] de
In Arbeitspaket 3 wird die Oberflächenendbearbeitung von additiv gefertigten Bauteilen untersucht. In der additiven Fertigung ist Oberflächenbearbeitung ein sehr wichtiges Thema, da nicht bearbeitete Teile üblicherweise eine schlechte Oberflächenqualität aufweisen, die zu verminderter Festigkeit und Lebensdauer führen kann. Additiv gefertigte Bauteile zeigen aber häufig Hinterschnitte, Aushöhlungen oder feine Strukturen, deshalb sind selten konventionelle Oberflächenbearbeitungen wie Schleifen oder fräsen möglich. In diesem Arbeitspaket wird das Plasmaelektrolytische Polieren (PeP) angewendet. Dafür müssen optimale Prozessparameter gefunden werden, die z.B. die EBM-Ermüdungsproben aus Arbeitspaket 2 bestmöglich glätten. Die so verbesserte Oberfläche wird z.B. zerstörungsfrei mit optischen Mitteln oder durch Querschnitte und REM-Aufnahmen charakterisiert.
Am IMKF-AM werden im Arbeitspaket 3 außerdem Proben und Bauteile mit dem selektiven Laserschmelzen gefertigt.
Die additive Fertigung ist noch ein junges Feld, wird in der Industrie jedoch schon an vielen auch lebensdauergefährdeten Bereichen eingesetzt. Daher ist es wichtig, nicht nur genormte Proben zu untersuchen, sondern auch ein realistisches Bauteil. Die additive Fertigung wird oft für topologieoptimierte Bauteile eingesetzt, weil deren Geometrie meist nicht konventionell gefertigt werden kann – Topologieoptimierung und additive Fertigung bedingen einander.
Im Arbeitspaket 4 werden die aus den Arbeitspaketen 1-3 gewonnen Erkenntnisse auf ein praxisnahes Bauteil angewendet. Dieses Bauteil wird fertigungs- und lebensdauergerecht topologieoptimiert. In die numerischen Untersuchungen fließen die in Arbeitspaket 2 ermittelten Materialkennwerte und die in Arbeitspaket 3 erreichten Erkenntnisse zur erwartbaren Oberfläche ein. Anschließend werden die Bauteile mit EBM und SLM gefertigt und in einem eigens entwickelten Prüfstand auf ihre Betriebsfestigkeit geprüft. So können die auf Probenniveau gewonnen Erkenntnisse mit praxisnahen Anwendungen direkt verglichen werden.
Ansprechpartnerin: Jenny Köckritz (Jenny [dot] Koeckritz [at] imkf [dot] tu-freiberg [dot] de)
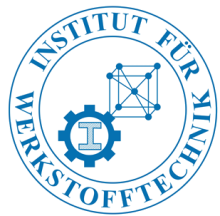
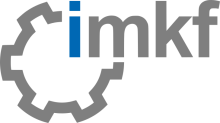
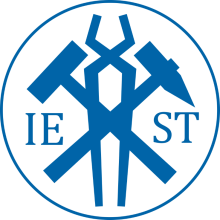