Shaping Glass in the 21st Century: Additive Manufacturing of Transparent Glass Objects
The Glass3D project is researching new materials and methods for the production of optically highly transparent glass objects using additive manufacturing technologies. There is a high demand for new manufacturing technologies, particularly in the production of technically functional glass objects and complex glass structures. The project focuses on the manufacturing technologies binder jetting (BJT), direct melt printing (DMP) and vat photopolymerisation with curing by exposure to ultra violet light (VPP-UVM). The three processes differ fundamentally in the form of the raw material and the respective bonding mechanism:
- In BJT, the powdered glass particles are cross-linked by a liquid binder. The green body generated layer by layer must then be sintered.
- In VPP, the glass body is generated by means of localised solidification of monomer liquid exposure to UV light. Sintering of the green body is also necessary here.
- In DMP, the glass raw materials are melted in a crucible and extruded locally through a nozzle. Subsequent sintering is not necessary.
With previous DMP, only coarse, large objects can be produced. The glass raw material has to be prepared in advance by crushing, grinding and sieving, which involves high energy costs and material wear. To increase energy efficiency, the glass raw materials should therefore be melted and purified directly in the 3D-printer.
BJT and VPP can be used to produce much finer structures with high resolution. BJT also impresses with its high printing speeds. For the production of optical glass components, new developments of the base materials, matrix-binder compositions for BJT and resins for VPP, are required. Extensive new and further developments on the machine side are required for all technologies.
Additively manufactured glass objects often have internal defects such as bubbles and interfaces, which cause unwanted light refraction and severely impair the mechanical properties and transparency. The Glass3D project addresses the reduction of these defects and enables the flexible production of complex, transparent glass components through cross-departmental and cross-national cooperation.
Tasks IMKF
- Process development of binder jetting for glass
- Process development of direct melt printing for glass
Project partners
TU Bergakademie Freiberg, Institute for Glass and Glass Technology (IGT), Germany
Hebrew University of Jerusalem (HUJI), Israel
Project duration
06/2021 – 12/2024
Meike Denker, M.Sc.
meike.denker@imkf.tu-freiberg.de
03731/39 2526
Agricolastraße 1
Karl-Kegel-Bau
09599 Freiberg

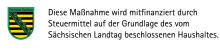