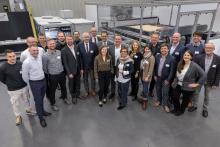
State Minister Schmidt inaugurates innovative multi-material printer for sustainable materials
The SAMSax simulation laboratory at TU Bergakademie Freiberg has been researching how 3D printing can return residual materials to the product cycle for over two years. What has so far been trialled on a small scale with modified printers can now be put through its paces on a large scale. Today (16 December 2024), a milestone was set for the circular economy and a masterpiece of Saxon mechanical engineering was put into operation: Minister of State Thomas Schmidt inaugurated an innovative, open-material printer designed to process a variety of organic and inorganic residues as well as industrial and agricultural by-products into larger objects. The development was carried out in close cooperation with C-marx GmbH Chemnitz, with over 50 residual material analyses and numerous test prints providing important findings.
State Minister Thomas Schmidt: "The SAMSax simul⁺real laboratory gives small and medium-sized companies easy access to expertise and infrastructure in the field of sustainable and future-proof production. Over 200 partners now belong to the SAMSax network. The technology of the new printer makes it possible to optimally utilise the recycling potential of residual materials from industry and agriculture. I am delighted that Saxony is now at the forefront of additive manufacturing and wish it many successful applications."
The new printer is truly unique and makes it possible to process a wide range of materials. For example, powdery organic and inorganic waste from agriculture or industry, such as wood, chaff straw, mining residues or fruit stones (e.g. from apricots), which previously remained unused, can be processed into new materials and reused in production. The technology makes it possible to maximise the recycling potential of residual materials from industry and agriculture. These materials are converted into materials that can be further processed in industry - a significant contribution to reducing waste and promoting the circular economy. The process has been successful, for example, in the creation of theatre props, packaging inserts or applications in mould making.
Prof. Dr.-Ing. Henning Zeidler, Project Coordinator of SAMSax and Head of the Chair of Additive Manufacturing at TU Bergakademie Freiberg, explains: "Additive manufacturing is a key technology that still offers enormous potential for the future. By using sustainable materials from regional residues, we can not only optimise the use of resources, but also develop new applications and products." For years, the professorship has been pursuing the goal of converting previously unused or only energetically utilised raw materials into high-quality, environmentally friendly and cost-efficient products and components.
Background:
SAMSax stands for Sustainable Additive Manufacturing in Saxony. This is the colloquial term for 3D printing, which usually involves the use of special metals, plastics and resins. The project was one of the three winners of the 2021 model project call "simul⁺Reallabore" organised by the Saxon State Ministry for Regional Development. The SAMSax real-world laboratory is being supported with almost 1.7 million euros from the Saxon State Ministry for Regional Development via the simul⁺InnovationHub.
The SAMSax project is an interdisciplinary project being implemented by the Technische Universität Bergakademie Freiberg (Chair of Additive Manufacturing) in collaboration with the Technische Universität Dresden (Chair of Wood Technology and Fibre Materials Technology) and the Technische Universität Chemnitz (Chair of Ergonomics and Innovation Management). Since the start of the project in spring 2022, an innovation community of over 200 partners from research, industry and public institutions has formed. The partnerships are to be further expanded in order to strengthen the circular economy in Saxony and open up new sources of value creation. The SAMSax living lab will run until June 2025.
Original message:
https://www.medienservice.sachsen.de/medien/news/1082686