The substances to be deposited are vaporised in a high-vacuum chamber. They are deposited onto the substrate without a chemical reaction taking place.
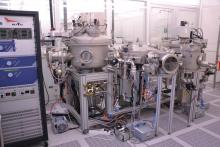
Sputter system
The material to be deposited is provided in form of a so-called target. From this, particles are transferred into the gas phase by means of sputtering and deposited on the sample.
Different to chemical vapour deposition (CVD), no chemical reaction takes place during physical vapour deposition (PVD). The substances in question are transferred into the gas phase using various methods and are deposited onto the sample. In the sputtering process (cathode sputtering), high-energy ions are shot from a plasma onto the target in a high vacuum. This causes particles from the target to enter the gas phase and deposit on the sample. By adding a reactive gas (O2, N2), layers of substances that are formed during the process can also be deposited.
The Bestec sputtering system has a preparation chamber for pre-cleaning using plasma and two process chambers. These each allow RF (radio frequency) and DC (direct current) and substrate heating up to 600 °C. We use sputter chamber 1 for the deposition from metallic targets (2 sources of 8 inches each), preferably aluminium and titanium. Sputter chamber 2 has three sources (3 inches each) in a confocal arrangement. This allows for simultaneous sputtering from several sources or the deposition of different thin layers in alternating sequence. The layer thicknesses can be monitored in situ using oscillating crystals. The vapour deposition system has a high-vacuum chamber in which the samples are fixed in the upper part of the chamber with the upper side facing downwards. Crucibles containing the materials to be vaporised are located some distance below. These can be metals, non-metals, oxides or organic substances. If the boiling point is relatively low, resistance heating is sufficient; higher-boiling materials can be vaporised using an electron beam. Due to the long free path between the source and the sample, the coating is very directional. An oscillating quartz crystal measurement is used to monitor the coating thickness.
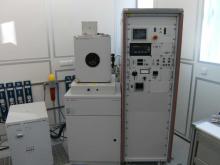
Vapor deposition system
The substances to be deposited are prepared in metal crucibles and vaporised using resistance heating or an electron beam. They are then deposited unchanged and, thanks to a longer free path, very directionally on the substrate.
Die Bedampfungsanlage besitzt eine Hochvakuumkammer, in der die Proben im oberen Bereich der Kammer mit der Oberseite nach unten befestigt werden. In einigem Abstand darunter befinden sich Tiegel mit den zu verdampfenden Materialien. Dies können Metalle, Nichtmetalle, Oxide aber auch organische Stoffe sein. Bei relativ niedrigem Siedepunkt reicht eine Widerstandsheizung aus, höher siedende Stoffe können mittels Elektronenstrahl verdampft werden. Durch eine große freie Weglänge zwischen Quelle und Probe geschieht die Beschichtung hier sehr gerichtet. Für das Monitoring der Schichtdicke wird eine Schwingquarzmessung genutzt.
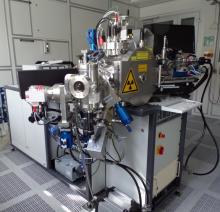
Pulsed laser deposition
Here the substances are transferred from a target into the gas phase by use of a pulsed laser beam. In this way, it is also possible to vaporise mixtures of substances and deposit them in the same stoichiometry.
The PLD system (Pulsed Laser Deposition) is operated in the cleanroom laboratory in cooperation with the Fraunhofer Technology Centre for High-Performance Materials. Here, particles are transferred from a target into the gas phase in a high vacuum by irradiation with pulsed high-energy laser light and are deposited on the sample. The special feature here is that all substances contained in the target are vaporised at the same time; there is no "distillation effect" that would cause a separation of substances according to boiling points. In this way, for example, mixed oxides can also be deposited as solid solutions. Such material systems are very interesting as insulator materials.
The owner of this device is the Fraunhofer Technology Center for High Performance Materials. As part of a cooperation agreement, it was installed in the Central Cleanroom Laboratory and is operated here.