While wet chemical etching processes are uniform in all dimensions, plasma etching is able to remove material, particularly in depth. This does not reduce the lateral structure resolution.
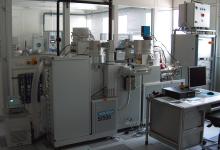
Plasma etching cluster
This system enables reactive ion etching in two separate chambers with chlorine- or fluorine-based gases.
In plasma etching, reactive gas molecules are ionised in a plasma. A high-frequency field causes these ions to reach the sample at high speed. In addition to the etching effect caused by reactive ions, a physical layer removal (sputter effect) also takes place due to inert gas particles.
The CCL has an etching cluster from the manufacturer Sentech Berlin with two chambers for substrates up to 150 mm in diameter and ICP plasma source SI 500. The ICP power is 100 - 1200 W; that of the high-frequency coupling 0 - 600 W (both unpulsed, 13.56 MHz). Chamber 1 allows processes with Cl2, BCl3 and HBr at substrate temperatures of 0 - 80 °C (cryo-circulation cooling), with conversion to air cooling up to a maximum of 300 °C. Chamber 2 is intended for processes with CF4, CHF3, C4F8 (currently not connected) and SF6. A circulating air chiller is currently installed for substrate cooling, which enables 30 - 80 °C. A conversion to cryo-circulation cooling or air cooling - see above - is possible. It is also possible to operate with liquid nitrogen for -150 to -80 °C. N2, O2 and Ar are available as carrier gases for both reactors; the pressure range is 0.2 - 10 Pa. The processes can be monitored in situ using a laser interferometer and an emission spectrometer.
Plasma-enhanced atomic layer etching
While atomic layer deposition (ALD) involves a very defined build-up of layers deposited on top of each other, layers are also removed or thinned in a defined manner here.
The PE-ALE module (Plasma Enhanced Atomic Layer Etching) is part of the deposition cluster (PE-CVD and PE-ALD). Similar to atomic layer deposition, where layers are built up very precisely and slowly, this is done here during removal by plasma etching. A real-time monitor, a laser interferometer and an OES (emission spectrometer) are available for process monitoring.
The owner of this device is the Fraunhofer Technology Center for High Performance Materials. As part of a cooperation agreement, it was installed in the Central Cleanroom Laboratory and is operated here.