How can the refractory industry be decarbonised? In other words, how can processes in which steel, cement and ceramics are produced become more climate-friendly? Yesterday, experts met at the 14th Freiberg Refractories Forum to discuss this topic. The Freiberg Refractories Forum was chaired by Professor Christos Aneziris. We asked him in advance why decarbonisation has become so important for this industry sector.
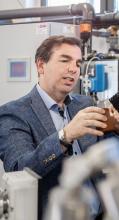
In conversation: Professor Christos Aneziris
Why is decarbonisation the theme of the Refractories Forum this year?
It's an important topic because our industries have to deal with very high temperatures. That means we need a lot of energy. In addition, we also have a lot of CO2 that is released in our raw materials. This means that if we are talking about decarbonisation, then we need to tackle the electrification of high-temperature processes. That means plasma technologies, microwave plasma technologies, electric heaters, high-temperature heaters, for metallurgy, for the chemical industry, for the cement industry. That means a broad spectrum, because all processes that take place above 600 degrees Celsius up to 2000 degrees Celsius are very important for us. These are strategic industries for Germany, for Europe. We are here in this Freiberg Refractory Forum, industry people and university people, and we are trying to cover the whole spectrum of hydrogen, ammonia and the corresponding materials that are needed, i.e. high-temperature materials, our materials, the refractory materials, but also the plasma technologies or hybrid firing technologies, so it may be that I switch with a plasma burner and then comes the electrical line and then the hydrogen burner. It depends on which atmospheres provide the added value for the final properties of the end product. Because we can not only save CO2 with the new hybrid firing technologies, we can possibly improve the properties of the new end product.
What are the alternative materials of the future?
We are not talking about alternatives, but rather we are trying to make the future more sustainable in terms of process technology. This means greater efficiency, less CO2, and multifunctionality. We are constantly trying to functionalise our materials. It is no longer the simple ceramic, but a high-temperature composite material or material composite that optimises a process. At the end of the day, this means that here in Freiberg we not only make classic ceramics, but also the marriage of metal and ceramics, of refractory metals and refractory ceramics, i.e. refractory composite materials for the energy transition. You talk about cars, but you forget that at least 10 kilograms of refractory are used per tonne of raw steel. You talk about aeroplanes or cement production, and you forget that the refractory lining materials that help shape these high-temperature processes like blood vessels determine the quality and efficiency of the end products, these are our invisible, silent heroes.
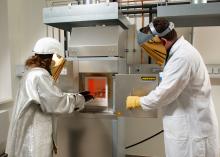
When I think of the car, what parts are related to the refractory industry?
When I think of the car, we also find ceramics there. Piezo ceramics, capacitors, resistors, in your mobile phone alone there are more than 30% ceramics, regardless of the glass, which is the foil on top. Ceramics accompany us constantly in our lives, at home, when travelling, at work. Ceramics are produced in a high-temperature process, and making these high-temperature processes more sustainable is a focus here in Freiberg.
What is the CO2 footprint of this industry?
If I compare it to the steel industry or the cement industry, it's a different world. Ceramics are much smaller than this sector, but they not only contribute to CO2 generation through their manufacturing process; functional ceramics as energy converters or in storage materials or as high-temperature electrode materials can make an essential contribution to energy transformation. Among other things, we are trying to electrify high-temperature processes and, not to forget, we are also trying to recycle. Recycling makes a very significant contribution to CO2 reduction. Our TU Bergakademie Freiberg is a recycling university, a recycling academy. Using the DFG Research Training Group 2802 as an example, basic scientific findings are being developed that enable both recycling, i.e. reuse in similar high-temperature materials, and upcycling, i.e. the material upgrading of refractory materials in metallurgical processes.