Increased efficiency in component design through the use of damage mechanics simulation methods
When designing a component in machine, plant and vehicle engineering, it has to be demonstrated, that it can withstand the loads to be expected in operation and can be run safely. In this process, computer simulation-based methods are increasingly replacing complex and cost-intensive experimental verification and thus make a significant contribution to increased efficiency and faster development cycles.
Damage-tolerant design ensures that defects that may occur during manufacture or operation due to material fatigue or corrosion do not lead to the failure of a component during operation.
Damage-tolerant design is mandatory in many safety-relevant areas, while in other areas it allows for more efficient use of materials. The damage-tolerant design by means of conventional fracture mechanics methods is, however, in some cases highly conservative. This means that the danger from defects is overestimated, so that dimensions and thus the weight of components are overdimensioned, potentially load-bearing components are are unnecessarily discarded or maintenance intervals are set too short.
In principle, damage-mechanical computer simulation methods allow to make more accurate predictions about the criticality of material defects and failures. However, such simulations require iterative calibrations on the basis of special tests and thus a high degree of special expertise.
The damage mechanics computer simulation methods developed at the TU Bergakademie Freiberg can be easily implemented and calibrated using a step-by-step procedure based on standard tests, which has already been successfully demonstrated for certain steel grades.
The aim of the validation project is to test these damage-mechanical simulation methods and the developed calibration procedure on a broad data basis and to make them usable to small and medium-sized companies in the form of a standard that is simple and safe to use. The resulting more precise component design reduces the material consumption for new products or allows to increase the intervals between cost-intensive maintenance work at the same high level of safety.
Publications
- A. Seupel, G. Hütter, M. Kuna, On the identification and uniqueness of constitutive parameters for a non-local GTN-model, Engineering Fracture Mechanics 229 (2020) 106817.
- G. Hütter, T. Linse, U. Mühlich, M. Kuna, Simulation of Ductile Crack Initiation and Propagation by means of a Non-local GTN-model under Small-Scale Yielding, International Journal of Solids and Structrures 50 (2013) 662-671.
- D.R. Pham, O. El Khatib, A. Seupel, G. Hütter, B. Kiefer, Iterationslose Bestimmung der Parameter des Gurson-Modells aus zwei genormten Versuchen, DVM-Bericht 254 (2022), 43-52
- O. El Khatib, G. Hütter, R.-D. Pham, A. Seupel, M. Kuna, B. Kiefer: A non-iterative parameter identification procedure for the non-local Gurson-Tvergaard-Needleman model based on standardized experiments, International Journal of Fracture 241 (2023) 73-94
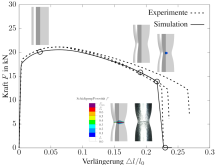
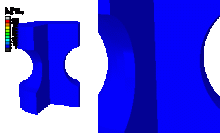
Download the implementation
The implementation of the non-local GTN model is available via the UMAT interface in Abaqus/Standard and via the VUMAT interface in Abaqus/Explicit. In the UMAT interface, the local GTN model is available as a special case (which is included in Abaqus/Explicit as standard).
Zip download
Funding
This research project was financed from 05/2021 to 10/2022 under the project number 100544457 with funds from the European Regional Development Fund (ERDF) and from tax revenue on the basis of the budget approved by the Saxon State Parliament.