Um Stahlteile in Form zu bringen, sind verschiedene Umformschritte notwendig. Gerade beim Warmumformen ist der Weg zum fertigen Bauteil mit hohem Energieeinsatz verbunden: Das Metall muss erhitzt werden, um es weich und formbar für das Walzen zu machen. Grund genug für die Projektpartner des Forschungsprojekts SiPro (Simulationsbasiertes Eigenschaftsdesign entlang der kombinierten Prozesskette Ur- und Umformtechnik), die damit verbundenen Prozesse durchgängig abzubilden, um zusätzliches Energiesparpotenzial zu heben. Außerdem nimmt SiPro die Fertigungsqualität unter die Lupe, denn auch weniger Ausschuss hilft, unnötigen Energieeinsatz zu vermeiden und die CO2-Bilanz des Stahlteils zu verbessern.
Gemeinsames Ziel der Projektpartner ist es, die Prozesse vom Stahlguss bis zum fertigen Bauteil als optimierten digitalen Zwilling virtuell abzubilden. Dafür analysieren sie die Fertigungsschritte mit einer simulationsbasierten Prozesskettenoptimierung. Gelingt es damit, die Energieeffizienz insgesamt zu steigern, könnte der ökologische Fußabdruck der Umformverfahren deutlich reduziert werden.
Derzeit gehen die Projektpartner davon aus, dass der Strom- und Gasverbrauch entlang der gesamten Prozesskette Warmmassivumformung um bis zu 10 Prozent reduziert werden kann. Bezogen auf die deutsche Jahresproduktion von Walzstahl von rund 30 Millionen Tonnen, könnte das theoretische Einsparpotenzial damit bei rund 4.920.000 Gigajoule pro Jahr liegen. Dies entspricht etwa 1.367 Gigawattstunden – und damit dem durchschnittlichen Jahresstrombedarf von fast 400.000 Privathaushalten.
Von der Simulation zur nachhaltigen Prozesskette
Im Projekt werden die entwickelten Modelle durch den Abgleich der Prozesssimulationen mit Validierungsversuchen bestätigt. Gleichzeitig werden Prozesse der Industriepartner messtechnisch digitalisiert, um die entwickelte Simulationsschnittstelle zwischen Gieß- und Umformprozessen an realen Industrieprozessen zu testen. Der digitale Zwilling liefert zusätzliche Informationen, die den Projektpartnern technologische Vorteile verschaffen.
Die entstehende Prozesskettensimulation wird genutzt, um die verschiedenen Fertigungsschritte der Wärmebehandlung und Umformung zu optimieren. So will das Team die Verarbeitungstemperaturen und Prozesszeiten reduzieren, ohne die Bauteileigenschaften zu beeinträchtigen. Zudem werden Möglichkeiten zur Qualitätsverbesserung und Ausschussreduzierung aus den Simulationsergebnissen genutzt.
Abschließend testen die Partner die optimierten Randbedingungen in industriellen Prozessen, um das CO2-Einsparpotenzial verlässlich zu beziffern.
Physikalische Simulation der Umformprozesse
Die Forschungsschwerpunkte des Instituts für Metallformung der TU Bergakademie Freiberg im Projekt beinhalten vor allem die Ermittlung von Werkstoffkennwerten für die Simulationen sowie die instrumentierte physikalische Simulation der Schmiede-, Walz- und Ziehprozesse innerhalb des Gemeinschaftsprojektes. Das Bild zeigt einen Snapshot der Temperaturmessung mittels Thermografie während des Schmiedens eines Gussblockes auf der 10 MN-ölhydraulischen Presse des Institutes.
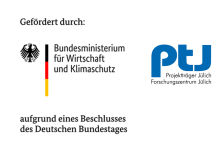
Projektpartner von SiPro
- Fraunhofer-Institut für Werkzeugmaschinen und Umformtechnik IWU
- TU Bergakademie Freiberg
- TU Chemnitz
- Stahlzentrum Freiberg e.V.
- Rosswag GmbH
- Georgsmarienhütte GmbH
- Mannstaedt GmbH
- Schmiedewerke Gröditz GmbH
- GSA Gesenkschmiede Schneider GmbH
- MAGMA Gießereitechnologie GmbH
- Hexagon Manufacturing Intelligence GmbH
- Karl Diederichs GmbH & Co. KG