For the first time, nine research partners are developing and comparing processes for the recovery of the active material lithium iron phosphate (LFP) - both in the direct recycling of the entire cathode material and for the reutilisation of its individual raw materials. The aim of the DiLiRec research project is to develop economically attractive processes for the reuse of sustainable cell chemistry and its components in battery production. Under the leadership of Prof Urs Peuker, a team from the Institute of Mechanical Process Engineering and Processing Technology at TU Bergakademie Freiberg is investigating a central aspect of the overall project's research questions.
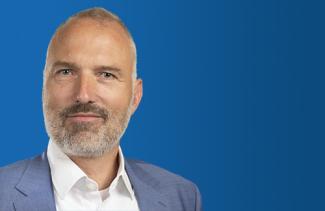
Professor Peuker, DiLiRec is a research project involving nine partners. What role does TU Bergakademie Freiberg play in this network?
Our task is to extract the coating materials, in particular the battery cathode, in as pure a form as possible. This material is then the starting point for reprocessing and reintroducing it into new batteries. For this purpose, we receive dismantled battery components, so-called electrode coils, from the project partners. These consist of two differently coated metal foils placed on top of each other, which are rolled up to fit into the battery cell. This is why many batteries are cylinders. Our task now is to obtain the coating of one of the foils with the highest possible purity and yield. The target material is iron phosphate, which serves as the cathode of the battery and stores the lithium ions when discharged. The iron phosphate can be imagined as very fine particles with a characteristic length of just 1 micrometre, making them significantly finer than other battery materials.
What makes the recycling of lithium-ion batteries relevant right now?
The recycling of lithium-ion batteries is important in several respects and is necessary from an economic, strategic, regulatory, technological and environmental perspective. Firstly, battery materials are not completely harmless. National and European legislation has therefore created a framework for how these materials are to be handled safely. In addition, various chemical elements contained in batteries are so-called critical raw materials. Critical raw materials are materials that have both high economic relevance and limited availability. The limited availability or supply risk can be influenced by various factors, including not only technological but also political factors. Sustainable battery recycling protects our environment by not releasing the battery materials and also makes it easier for us to access critical raw materials as they are kept in circulation.

Why is lithium iron phosphate from lithium iron phosphate batteries not yet recovered from old batteries?
Unfortunately, it is not economically attractive to recycle battery cells with lithium iron phosphate. Compared to lithium-ion batteries with a cell chemistry based on nickel, cobalt and manganese, the cell chemistry based on iron and phosphorus used here is significantly cheaper and therefore less valuable for the recycling business model. For regulatory and environmental reasons, the recycling of lithium iron phosphate batteries is of course still necessary. However, there are currently fewer research and development efforts for these materials, so we also want to close a certain knowledge gap in this project.
The concept of direct recycling could potentially close the economic viability gap. This is because the functional materials of the battery are not broken down into their chemical components, but are chemically treated as functional materials themselves so that they can be reused directly. This significantly reduces the effort required and enables cost-effective operation.
Iron phosphate batteries have become very attractive in recent years, particularly for low-cost electric vehicles, but also as stationary storage systems, for example for photovoltaic systems. We therefore expect a higher proportion of this type of battery in recycling material streams. We are therefore looking forward to the challenge and hope to develop interesting findings together with the project partners and hopefully arrive at a good technological solution.
Further information on the project
The DiLiRec research project has a total volume of 4.7 million euros. It is being funded by the Federal Ministry of Education and Research (BMBF) with around 2.7 million euros as part of the "Increasing efficiency and utilising synergy effects in battery cell production for electromobility (SynBatt)" funding measure (funding reference: 03XP0549).